
Beauty
Is Hair-Skin-Nail Minimalism the New Maximalism for 2025?
Trends come and go, but 2025 feels like the year we’re turning the whole concept of “trends” on its head. …
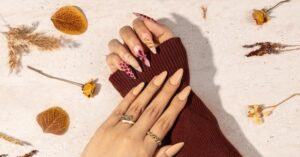
Is Hair-Skin-Nail Minimalism the New Maximalism for 2025?
Charlotte Miller
Trends come and go, but 2025 feels like the year we’re turning the whole concept …
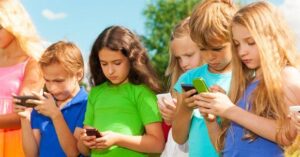
Why Are Your Kids Glued to Screens All Summer? Here’s How to Break the Cycle Without Losing Your Mind
Charlotte Miller
Summer break. That sweet, sprawling stretch of freedom where kids are supposed to run wild, …
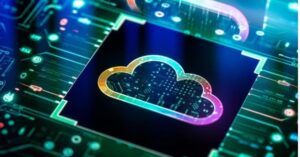
What Are Cloud-Based Systems Really Doing for Business? Here’s How They’re Revolutionizing Industries
Charlotte Miller
Cloud-based systems are reshaping how industries operate. From streamlining operations to unlocking new levels …

How Can You Decide Which Health Trends Actually Work for You?
Charlotte Miller
Health trends will always come and go faster than you can say “keto,” but how …
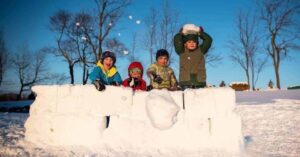
What’s the Midwest Hiding This Winter? You’ll Be Surprised
Charlotte Miller
Winter in the Midwest isn’t just about shoveling snow and dodging icy sidewalks. This region …

Is Hair-Skin-Nail Minimalism the New Maximalism for 2025?
Trends come and go, but 2025 feels like the year we’re turning the whole concept …
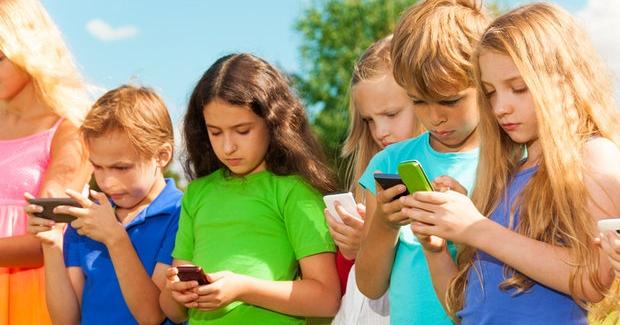
Why Are Your Kids Glued to Screens All Summer? Here’s How to Break the Cycle Without Losing Your Mind
Summer break. That sweet, sprawling stretch of freedom where kids are supposed to run wild, …